Boosting the performance in gearbox requires a novel gear tooth profile, parametric optimization, proper alignment, allowable backlash etc. The industries necessitates an unique approach to gear design with high quality, high strength to weight ratio material, longer fatigue life and high load carrying capacity. Research and development plays a critical role in industrial gears at each stage, starting from gear design with proper material selections and to improve the service life of the gearbox.
Finite element analysis allows the complete gearbox components to be modeled and evaluated virtually before it is fabricated and put in the real work environment. In recent years, the step up and step down gearbox are developing in the direction of high torque, high speed with less noise, vibration reduction and compact in size. During high speed running condition the gearbox experience higher contact and bending stress which leads to pitting and tooth breakage respectively.
Therefore FEA is used to determine the contact and bending strength of the gear drives to ensure the efficiency of the industrial gearbox with high load carrying capacity. In addition, the estimation of time varying mesh stiffness and transmission error to study the dynamic characteristics of gear drives under high power transmission. The methodology for estimating the stress and fatigue life through FEA is shown in Figure 1.
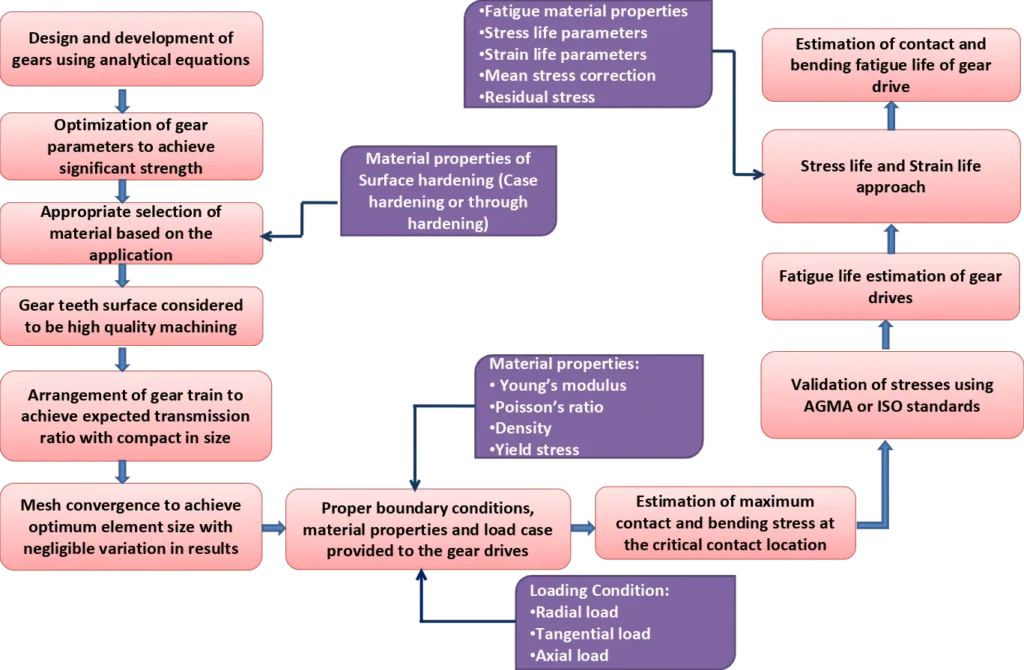
Failure modes on industrial gear
Failures in gears are classified as surface pitting failure, tooth breakage fatigue failure, scuffing, wear, plastic deformation and corrosion. Fatigue failure in gear drive is predominant which cause crucial damage to the complete mechanical system. Also, under high speed operation the gear tooth experience higher contact and root stress at the critical region with the dependence of temperature and misalignment.
The maximum contact stress at the critical contact tooth surface leads to contact fatigue failure which results in pitting and scuffing. Pitting leads to macro crack initiation and it propagate to cavities on tooth surface. Scuffing failure caused due to the adhesive wear between two contact surfaces which create spot welding and tearing. In addition, the fatigue wear caused due to the effect of asperities between the contact teeth regions will induce high plastic deformation.
One of the solutions for increasing the contact fatigue life is to decrease the limiting circle radius at the drive side which increases the radius of curvature at the single and double tooth contact region for normal contact ratio gears. FEA is used to determine the contact fatigue crack initiation life to predict the service life of gear drives. The maximum bending stress at the critical root of gear tooth profile leads to crack initiation and it propagate to tooth breakage.
The numerical analysis shall be carried out to estimate the stress intensity factor (SIF) at the critical root crack along the face width of gear tooth profile. For increasing the bending fatigue life, trochoidal profile shall be provided at the root for avoiding the interference with higher root strength. The trochoidal profile need to meet the involute profile at the point of tangency and that intersection point is limiting point. Similarly, the service life between the crack initiation and crack propagation is determined at the root of the gear.
Furthermore, the misalignment between the gear and pinion will reduce the effective contact region of tooth contact and increases the contact and bending stress which also leads to high vibration and noise inside the gearbox. Therefore, the estimation of contact and bending stress with fatigue life provide a great significance and trustable for designing a high transmission gearbox. The pictorial representation of contact fatigue failure and bending fatigue failure is shown in figure 2 and 3 respectively.
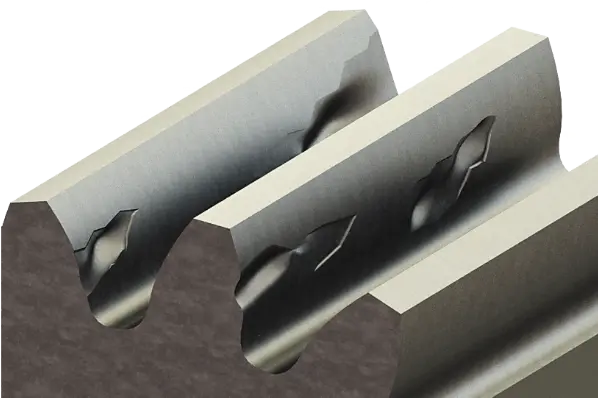

Finite element analysis on gearbox
The finite element approach is an effective tool for investigating the contact analysis of gear meshing and optimization. The estimation of maximum contact and bending stress at the critical region of the gear drives based on linear elastic analysis. Followed by fatigue analysis is carried out to estimate the contact and bending fatigue strength of the gear pair. A schematic representation (Fig.1) of the proposed computational contact and bending fatigue life estimation is separated into different stages.
In the first step, design and development of 3D gear models for on step up or step down gearbox with space constraint and transmission ratio. Also, the supporting components such as bearings, gear shaft, seals, bearing covers etc. shall be included. Figure 4 depicts the 3D Epicyclic gear with compound gear arrangement.

The second step is to provide appropriate material properties and boundary condition and load applied on the gear teeth. The force applied on the single tooth contact region is considered as the critical region which increases the contact and bending stress. Only tangential and radial force will act on the spur gear which causes bending moment on the shaft. The helical gear will experience tangential, radial and axial force which leads to bending in the perpendicular plane.
The applied torque in the gear is equal to the sum of the distributed forces. In gear teeth mating condition, the applied load will be shared based on contact ratio to single tooth point contact and double tooth point contact for normal contact ratio gears. The third step is to conduct the mesh convergence to attain optimum mesh quality. The FEA estimates the stress distribution along the mesh cycle and it is used to determine the maximum contact and bending stress at the critical region.
In the fourth step, the fatigue analysis shall be determined based on the combination of stress distribution data and fatigue material properties. The contact and bending fatigue life of gear drive is estimated using stress and strain life approach with the effect of mean stress correction, residual stress and notch factor. This fatigue analysis will predict and ensure the service life of gear drive. In addition, the optimization of important gear parameters will improve the contact and bending fatigue life of gear drive in order to achieve significant transmission ratio.
The gear parameters like module, pressure angle, transmission ratio, addendum modification factor, teeth number, pressure angle, helix angle, face width etc. can be optimized to achieve higher contact and bending fatigue life. Based on the parametric optimization the gear design should meet higher efficiency, reliability, load carrying capacity and compact in size. The von Mises stress and principal stress at the contact tooth surface and critical root respectively is shown in Figure 5 and 6. Also, contact and bending fatigue life of spur gear drive is shown in Figure 7 and 8.

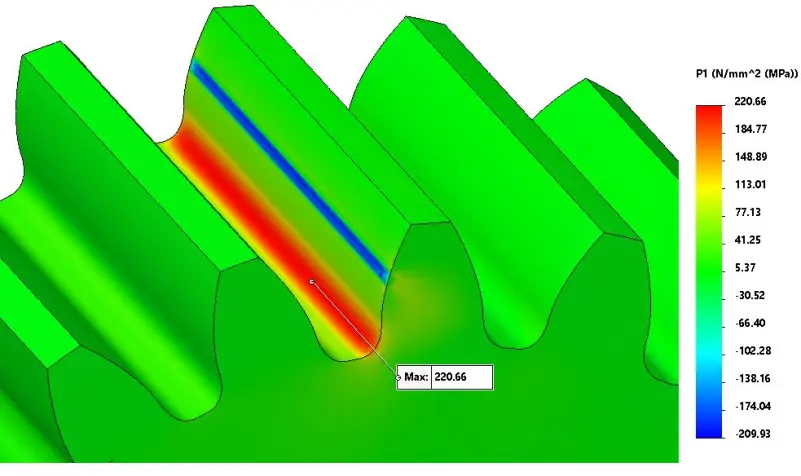

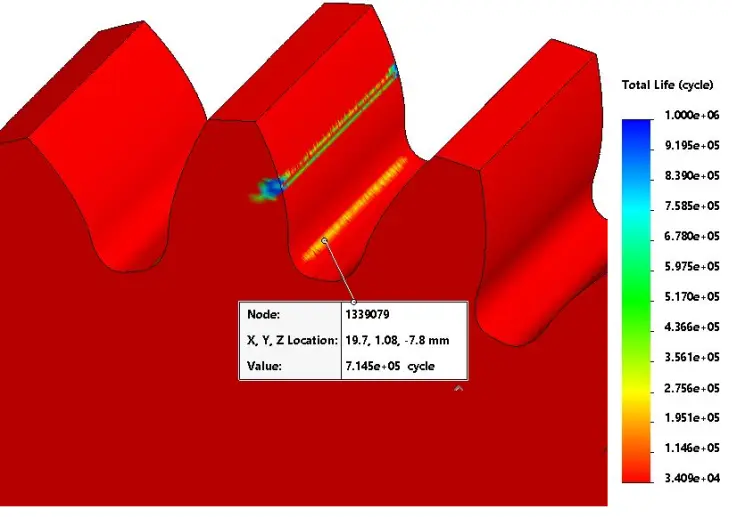
Furthermore, the heat generation due to friction is one of the major factors in gear transmission failure. The thermo-mechanical analysis shall be carried out to determine the deformation due to thermal effects, frictional heat flux under high load and thermal fatigue on gear drives. This thermo-mechanical analysis is important to check the stability and thermal failure on gears and gearbox components.
Also, the computational fluid dynamics analysis is used to study the splashing power loss and oil distribution inside the gearbox. Finally, the FEA results are validated with the analytical calculation based on gear standards or experimentally to check the simulation accuracy.
Summary
The accurate finite element analysis of gear strength in an industrial gearbox is required to ensure efficient performance, longer service life, and increased reliability. To optimize the gearbox design, simulation on stress analysis, fatigue, gearbox lubrication, thermal, acoustic, and vibration shall be carried out under various input speeds, torque, and friction factors. The engineers can choose an ideal gearbox with better performance with the aid of the finite element analysis.
The gearbox manufacturers will be able to maintain their competitive advantage in the market owing to this study, which will save costs and turnaround times.
The gear type selection, appropriate material selection, gear strength calculations, shaft selection and manual calculations, tolerance analysis and optimization, bearing selection, gearbox housing, centre distance, contact ratio, backlash, operating temperature, lubrication selection, design for life, design for safety, design for quality and gear design standards must all be taken into account during the entire gearbox design process. 2D manufacturing drawings with GD&T shall be done for complete gear box assembly with manufacturing tolerances. Finally, the correlation with gearbox prototype testing shall be carried out.
Thank you for Reading!
Author,
Dr.Rajesh S, Senior CAE Engineer | EGS Computers India Pvt Ltd.