Introduction
Sequential multi-physics is a modeling technique in which the simulation results from one solver (referred to as Upstream or Source) are used to drive a simulation with different or additional physics in another solver (referred to as Downstream or Target). A sequentially coupled multi-physics analysis can be used when the coupling between the physical fields in a model is only important in one direction. Stated differently, it is considered that the downstream outcomes have dependency on the upstream outcomes. A common use case is a sequential thermal-stress analysis, where-if thermal expansion is taken into account in a stress analysis, volumetric strain develops; however, the deformations calculated in the stress analysis do not appreciably change the thermal response. In such cases, a pure heat transfer analysis is the run as the upstream simulation. Since the current study does not alter the temperature fields from the upstream, they are predetermined when used for driving the analysis.
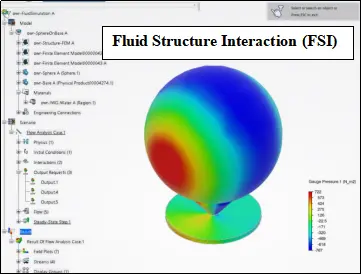
Supported Workflows
Sl.No | Analysis Type | Sequence |
1 | Sequential Thermal Stress | FMK → SSU |
2 | Sequential Fluid Structure Interaction | FMK → SSU |
3 | Thickness Mapping | SSU → SSU |
4 | Plastic Injection Molding | IME → SSU |
5 | Field Variable Mapping | SSU → SSU |
I have stated the different types of workflows that can be utilized to do any sequential multi-physics analysis. But let me try to explain with a targeted workflow so that It can be understood with our default sequential simulation capability and the other one with which we try to integrate other simulation roles in our 3DEXPERIENCE Platform.
Structures-Structure Thermal Stress Workflow
Built-in sequentially coupled thermal-stress analyses have been available in the structural apps for many years. This remains the preferred method for Structures-to-Structures sequential thermal-stress when applicable.
The new sequential multiphysics coupled thermal-stress workflow has some advantages and disadvantages as compared to the built-in workflow. Its capabilities will continue to be expanded through further development on upcoming updates.
Sequential Coupled Thermal-Stress Analysis (Built – In) | Sequentially Multiphysics Workflow: Thermal-Stress |
Same product used for thermal and stresssimulations. | Supports the same product, different products, empty products (orphan meshes) for thermal and stress simulations |
Single simulation object | Two separate simulation objects |
Full element support, including gaskets | Supports most three-dimensional continuumelements and non-composite three-dimensional conventional shell elements. No gaskets element support yet. |
Uses *TEMPERATURE Abaqus functionality. | Uses *EXTERNAL FIELD Abaqus functionality. (Has some memory usage benefits over *TEMPERATURE) |
Only supports SSU/SYE thermal results. | Supports thermal results from SSU, FMK, and IME. |
Sequentially Coupled Thermal-Stress analysis(Built-in) is a much simpler workflow than the new sequential multiphysics offering and should be used when applicable. In upcoming blogs I will discuss about the sequential workflow template, How to enable above stated workflows?, What are all the requirements? etc., with examples.
Stay Connected, Peace!!!!
Some of the 3DEXPERIENCE Roles mentioned in this blog are,
SSU – Structural Mechanics Engineer
FMK – Fluid Dynamics Engineer
IME – Plastics Injection Engineer
Thank you for Reading!!